RACL Plant Visit Notes (2.0) - 29th October 2023
Thanks to notes from other Colleagues (as@solidarity.in for one) who also visited the plant.
Maybe some of the details are useless for you as a reader, ignore them and take whatever makes sense to you.
Our movement through the plant was from 1- 6 mainly (as numbered on the map below)
It is a 26 Acre plant with ~50% utilized for actual production.
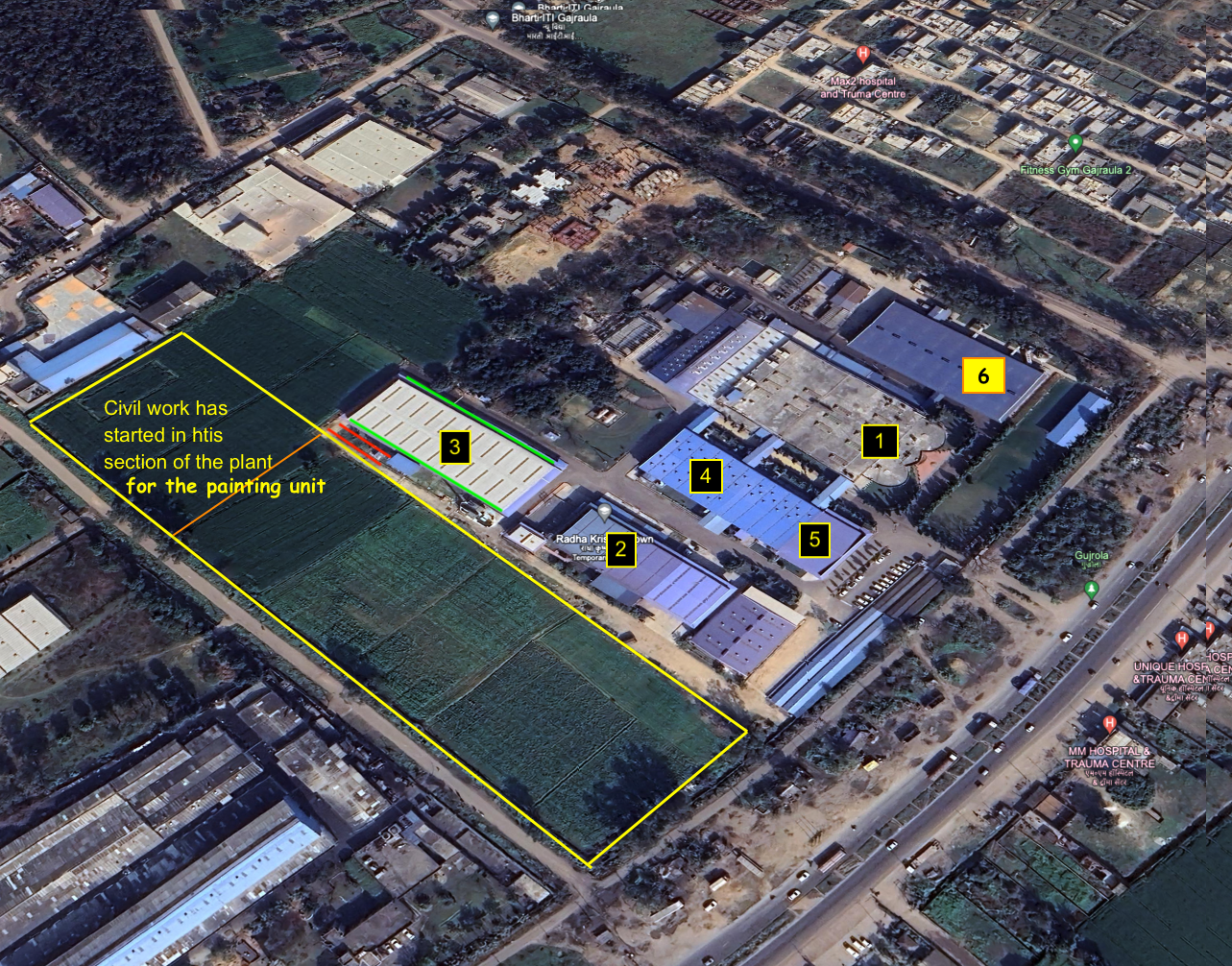
We were split into 2 groups of around 11 people each and one went clockwise 1-5 and the other group anti-clockwise.
But even before getting into the Plant Visit I want to mention a few things about the entire process leading up to the Visit itself.
Firstly, the management was extremely methodical with the application (fill out a form, enter how many shares you have etc) which seemed a little too much in my view.
Then, to those who received a confirmation they sent out an email which was again very precise about where to come, what the itinerary would be, contact details and getting our own SAFETY SHOES and having a proper DRESS CODE
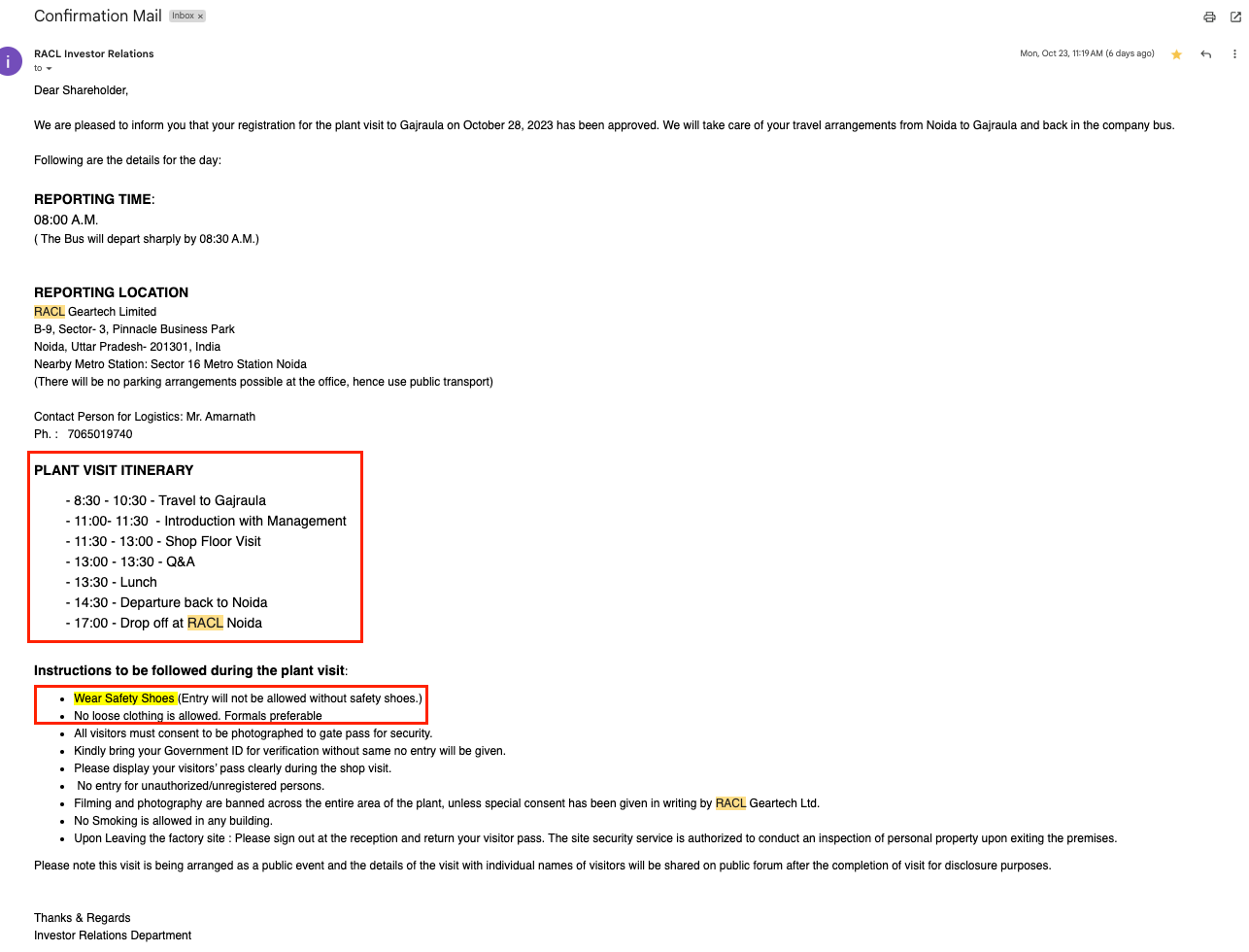
Once we got to the Gate, we waited for quite a bit as our photographs were taken, IDs were checked and a safety jacket (neon color) was provided which took a good 45 mins - 1 hr.
They even stuck stickers on our phone cameras both on the front and back to restrict photographs. Photography is restricted at most plant visits but being THAT PRECISE (stickers & All) AND METHODICAL was something even more experienced investors who were there were surprised.
Anyway, not sure how you should interpret it but it made sense post the visit WHY they were so, some may call it finicky about Everything.
" because how you do one thing is how you do everything" - Somebody.
Anyway, let’s get into the visit itself.
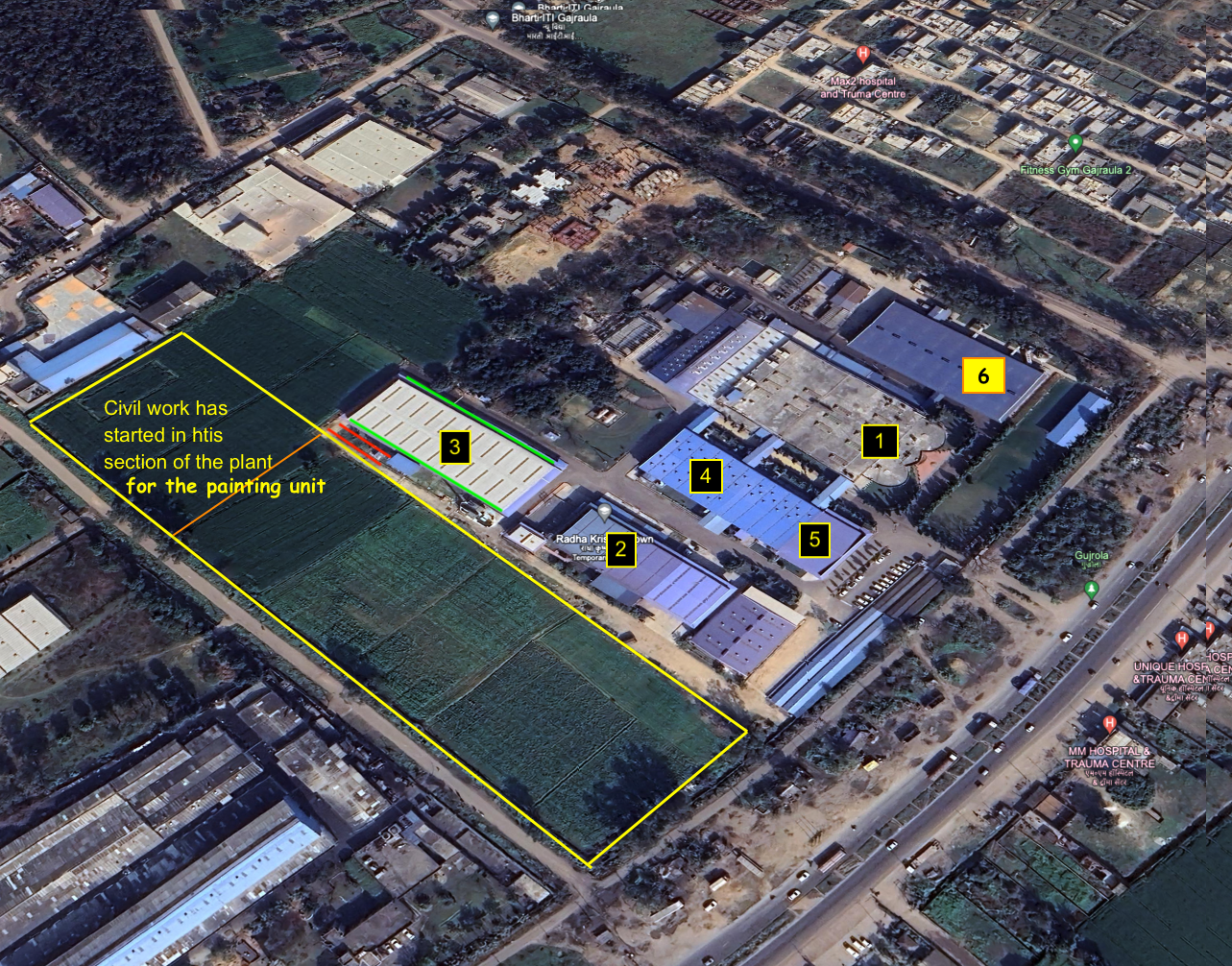
1 - CHETAK : The Main Building (built in 1983) - This is where the office is and where the boardroom etc is along with the oldest unit.
This unit is where the co’ focuses on products for the Agriculture and CV segment where relative to newer products (2W - premium etc) precision handling and cleanliness requirements are lower.
- Forging Unit - The forging unit is basically the beginning point since this is where the Raw material - Steel billets (for example) are beaten into the desired shapes for some of the products.
Domestic Steel mills supply the billets
Basically, billets are first cut using a machine (Indo-tech machines).
Then they are pressed (it’s literally a giant press) by a Forging press (chinese equipment) into the core part for what later most likely turns into something like the products highlighted below
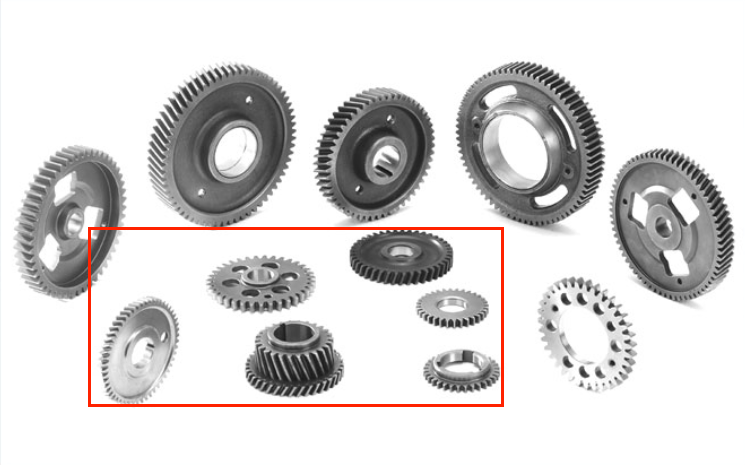
Co’ says that the forging design i.e - the shape of the press into which billets are pressed into are proprietary
Up to 15 Kgs of pieces can be forged in house.
The co’ has introduced a new product - Yokes, which was born out of a need.
One of the suppliers to the Customers (BMW vendor in France) had gone bankrupt and the co’ was approached by the Customer to forge these components.
The product has not yet taken off and currently contributes nothing to the Top line.
Basically Yokes are the component which make it possible for a bike wheels to rotate without a chain, its a new technology.
Despite these being ‘higher end’ forgings, It maybe (not 100% sure but likely) lower margin than the current consolidated margins of RACL consolidated.
It’s going to be a “high volume lower margin product”. Too early to say what the contribution will be to sales.
Approximately 50% of Forging requirements are met in house and the remaining are outsourced to 8 suppliers including MM Forgings etc
As for a high-level understanding of shifts from Europe, we are mostly aware that the Energy crisis in Europe had rendered steel production unviable which is reflected in super-normal steel prices over the last 2-3 years, which also shows up in increase in realization of most steel companies in India between 20-21 approx.
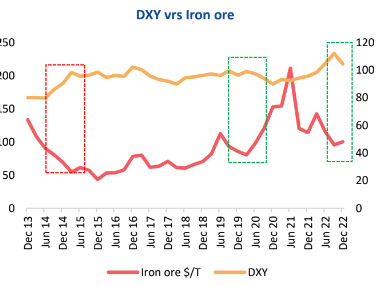
Steel Industry in India and Auto Ancillaries have been beneficiaries of this trend : Euro+1
We had met Menon bearings about 1.5 months back and the CFO/Director highlighted the same point. Their export orders had shot up during that period. And while there is increasing interest in Indian Auto Ancs, maybe the supernormal period of 20-22 may not be repeated.
Besides that, MAN Trucks & Buses is shutting their machining and forging unit for ICE and RACL believes that they will do all of these products by 2025 for MAN Trucks.
- OJAS - Built 2021 - Dedicated to ZF
This is the latest plant/unit built by the co’ and is completely dedicated to ZF
They have 7 products here which no one else makes for ZF. Exclusive supply (Thanks @Worldlywiseinvestors )
ZF is a Tier 1 Supplier to Mercedes, Aston Martin, BMW and they are present in both CV & PV
Co’ is in talks for a product which is patented and co’ is hoping to win that order.
RACL prefers to work directly with OE but made an exception given the ZF scale. Although, ZF was happy with the technological capabilities from Day 1 it took a while to crack ZF since they had never worked with an India player for Gears.
Another trend playing out with European Auto/Auto Component makers is that they are moving towards higher ‘value added’ and lower capital intensive work, such as Designing and consistently moving out of component manufacturing and focusing more on ‘subsystems’.
Whatever the difference is between the two, I wouldn’t know
but there is a trend playing out here which is likely to benefit RACL.
When we entered there was a showcase cabinet with all the parts made in this unit.
Mr. Prabh Meher Singh Explained one of the parts and why it was so difficult to make it.
It was a part used in a technology launched just in 2015-2016 by BMW (Verify) which basically balanced out the car when its turning so as to reduce jhatke from potholes etc.
Now, this part looks like a cylinder but the tricky thing is that the thickness of this cylindrical looking part varies throughout the length of the component.
This variability in the diameter/thickness along the length of the component is hard to achieve and even harder to consistently make the component within ‘tolerance limits’
Anyway, this unit was state of the art. Like really state of the art.
The data was centrally available on each machine on a software and ZF could monitor this data from Austria or wherever their monitoring unit is.
It was air-conditioned and machinery was automated and it was super clear, almost like a lab.
Although, I did not understand the nitty gritty of what was being done there lol it looked like it was an extremely high tech operation.
Prab mentioned how components made here (for BMW/ZF - verify) were subject to extremely stringent checks for example, one of their shipments/batch was rejected because it had a fingerprint on it
This unit gave business in 1 year what they had projected in 2-3 years time. During Covid, they enjoyed higher realization because of supply disruptions etc. (outlined earlier also)
As far Raw Material Costs are concerned, not everything is a pass through but Steel & Currency fluctuations are.
Competitors include Hero, Hi-tech Gears, Sundaram Fasteners etc
The 2 Red lines marked on the map show where Solar panel boxes were stacked, they seem to have been recently delivered.
Currently, the co’ consumption is 3.55 MW and 6% of Energy is from Renewables, and co’ is targeting this % to go up to 60%
This will reduce the Energy cost from ~ 7.5 Rs/unit to 3.5/unit
4. This was the heat Treatment plant and I think following the experience at least, in comparison it seemed not as exciting but this is where the components were, well, heat treated.
There were large furnesses which baked components so they could retain their performance at high temperatures.
5. Tejas : Built in 2011 is where 2W export parts were manufactured. Again, quite high tech looking like a lab.
All throughout the visit, Mr. Prabh mentioned the word ‘mindset’ one too many times almost as if it were a gospel and it made sense when you see it in the context of the process itself.
Every little detail counted and one needed to have a ‘mindset’ that allowed for such an operation to become high quality in the first place and remain high quality.
LUNCH @ Building 6 (on map)
The canteen was clean, and the food was absolutely top notch. There was a big banner on the wall recommending optimal sugar intake for Men & Women.
Post Visit management Q&A
The First question on whether co’ plans to raise funds through QIP etc was shot down by the Chairman and he was of the opinion that these things can be discussed in concalls also, let’s talk about the operations based on what you have seen etc.
But it was a great question, given that debt is 1.2X and because they plan to invest 250+ Cr over the next 2-3 years and CFO may or may not be enough to meet the Capex requirements (depending on the growth).
x
- The next question was on ICE vs EV and how well prepared the co’ was for that shift.
Management was of the opinion that because they are in the premium segment, it is going to be a while before they need to worry about that because the EV drive is going to first hit the economy segment for bikes, small CVs, passenger vehicles etc and they are not so much in the Commuter segment. Plus companies likes BMW (bikes) have given them a schedule till 2036 and they are very precise in terms of their planning and have been largely accurate thus far so that gives them comfort as far as substitution risk is concerned.
- Third question on how the idea of manufacturing ‘yolks’ came into the picture. This is where GCS explained how the Supplier to one of the customers went bankrupt and the customer asked them to make these parts.
As mentioned earlier these yokes are basically part of the tech that makes it possible for the rear wheels to turn without a chain.
Similarly, customer also asked co to provide a component with a ‘paint finish’ and they have hired consultants etc to setup a painting shop which is at par with Yamaha painting standards (shown on the map on top left side with a note)
That’s all. Then we took a picture and boarded our bus back to Noida.